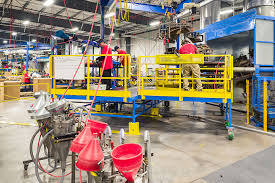
Exploring New Methods for Finishing Plastics Rotomolded Products
Plastics Rotomolding is among the most typical and cost-best ways to manufacture plastic-type material goods. It involves using a mold, which is stuffed with plastic material substance, warmed up in an cooker, and after that cooled until it has taken the shape from the mold. In this post, we will acquire a close look at the entire process of plastic-type material Rotomolding along with its many benefits.
The procedure of Rotomolding
The first step in rotomolding is usually to fill up a mold with powdered or water plastic-type substance. When the mold is filled, it can be positioned in an your oven where it will be warmed for a predetermined length of time. The high temperature brings about the plastic material dust to burn and increase until these are consistently distributed through the whole mold cavity. As the plastic-type material cools down, it begins to handle the contour of your mold, generating into its closing item when completely cooled down. This whole method might take between a quarter-hour to a few hrs for the way huge and sophisticated the thing getting shaped is.
Great things about Rotomolding
1 advantage that makes rotomolding so appealing to companies is it delivers increased design versatility than other developing processes as there are no difficult equipment or dies needed. Additionally, since there are fewer steps associated with generating a item, rotomolding is usually much more inexpensive than other approaches like injections molding or blow molding. This makes it suitable for creating smaller sized batches or prototype pieces quickly and easily without running into a very high cost per bit. Ultimately, given that molds may be used again repeatedly with little damage, rotomolding also allows suppliers to generate highly thorough physical objects with elaborate designs that would otherwise call for expensive generation tactics including 3D printing or machining.
Verdict:
Rotomolding offers plastics suppliers fantastic design flexibility combined with low fees and quick turnaround times—making it a stylish selection for generating tiny batches or prototypes efficiently and quickly without breaking their finances. It is also perfect for developing sophisticated models that might otherwise require pricey instruments or dies to generate making it well suited for producing custom made pieces swiftly while still saving cash total. For these reasons, rotomolding is becoming one of the more popular producing operations in use these days among plastics experts around the world!